Building boats from waste plastic (by hand) is a very meditative, but time-consuming business. Ask our volunteers. Our new tool speeds this process up by 30 days. One whole month. This means we can build even more boats!
‘Guys, you probably still have some scraps of old metal for us.’ With this question, Edwin went to visit Barend Schermer, director of Schermer Installation Technology in Hoorn. Three months later Clean2Anywhere had a new, handy tool: a ‘bending oven, fully powered by solar energy.
‘What is a bending oven anyway? And what should you do with it?’ Legitimate questions. If you build boats from waste plastic, a bending oven is a useful piece of technology. The workboats that we build, consist of about 500 parts. And each part is made by hand by our volunteers: young people and people with a refugee status who join us via Werksaam Westfriesland. These people often have been outside the labour process for a long time and while building boats, they discover what they are good at.
A very profitable tool
When making 500 parts by hand: you need many, many hands. And a lot of time. Especially the sawing and chiseling of the two dozen semi-circular frames (for those not in the know: the ‘ribs’ of the ship) is a time-consuming job. To give you an idea: one volunteer spends 1 to 1.5 day working on one frame. Multiply that by 24…
‘There should be an easier and faster way’, Edwin, founder of Clean2Anywhere, thought to himself. Earlier he had already outsourced the bending work of the keel beams of the previous workboats. ‘What if we could do that ourselves on site, preferably fully powered by solar energy?’
Like your own convection oven
This is where Schermer comes in: in collaboration with Edwin the company designed a machine in which the plastic frames can be heated. The bending oven works like a convection oven, like the one in your kitchen. We put the plastic planks in at 130 degrees for about seven hours. They do not melt. But due to the heat, the planks become bendable.
After taking them out, we immediately push them into a mold and fix them until they have cooled down. And as you can see, it takes a whole team and some teamwork to do that:
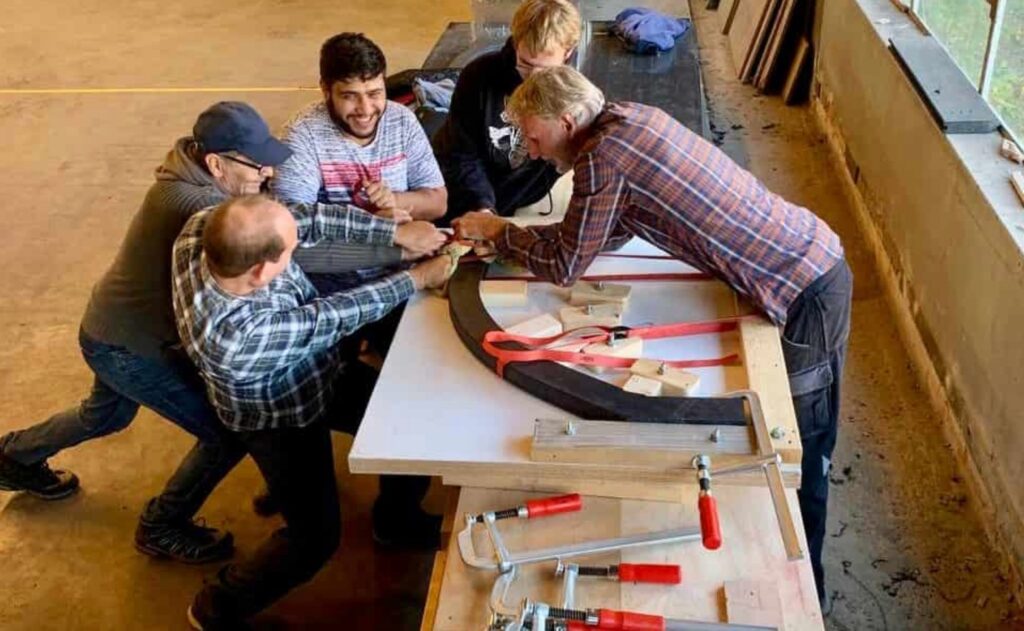
Bottom line: the bending oven is a good tool that saves our volunteers a lot of time and headache. It is expected that the construction of a single workboat can be shortened by 1 to 1.5 months, to be precise.
And the faster we can finish a workboat, the more boats we can build. The more people we can help with taking steps in their personal growth and creating themselves a new perspective. You see ultimately, what we do is not just about the waste plastic nor the boats, it’s about making a contribution to society.
No rocket science
And that is what connects Schermer to our project: we pursue the same goal. Barend: ‘I can show up with a bag of money, but it is much more interesting and fun to do something for a local organization. In this way we also stay informed of what’s going on with people in the area, for example with these young people and people with a refugee status. As a company in installation technology, we cannot do anything for them directly. But we can contribute something with something we are good at: technology. With this bending oven, we provide them with a good tool.’
What’s in it for Schermer’s company? Of course we know that the technology sector is in need of a huge amount of people. The bending oven is not a complicated device: learning to use it is no rocket science. ‘But it can be a good introduction to the profession,’ says Barend. ‘When putting such a machine in an exciting context, such as the construction of a boat, all of a sudden it attracts people’s attention. If you can get a few people excited for our business, that’s a plus.’